Maintenance of air filters
The filter service life is defined as the operating period between filter installation and filter replacement. It is determined by the following factors:
- Hygiene issues (e.g. microorganisms, fungal spores, odours)
- Optimisation of economic efficiency
- Reaching of the final pressure drop specified for the filter system in the ventilation system,
- Defective filter.
Filters should be changed considering the above-mentioned factors and the supplier’s maintenance plan. When replacing filters, it needs to be ensured that all filters across the entire duct cross-section are changed at the same time. Filters may only be changed with the system at standstill and by using personal protection equipment (clothing, gloves, class-P2 respirators). The used filters should be transported in big plastic bags.
Particularly when mounting new filters, utmost care shall be taken to prevent filter damage due mostly to the sharp edges of the slot. Contaminated filters should be handled with care, transported in a suitable, lockable package, and disposed according to local legislation. The connections between filter frames and partitions shall be cleaned, checked, and repaired, where required. The filter frames or the filter housing of the new filter as well as the sealing faces should be cleaned carefully prior to assembly. The new filter should be careful assembled as per assembly instructions.
Visual inspections of coarse and fine dust filters and particle measurements on particulate air filters of classes H and U must be performed at regular intervals to detect such defects. During maintenance, optical and/or electrical differential pressure gauges and indicators shall be checked for proper functioning. If testing a filter is impossible, it should be replaced after the period specified by the manufacturer.
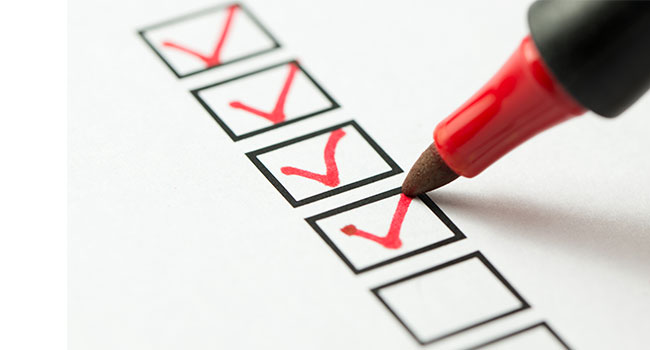
Transport and storage
To protect filters from contamination, they should be transported and stored only in their original packaging, preferably on pallets. Transportation should be done with care, avoiding any abrupt movement. Filter storage must be indoors according to manufacturer’s instructions (not outdoors), protected against rain and moisture, and at temperatures above the freezing point. The filters should be brought to the assembly site in their original packaging and should not be unpacked until immediately before assembly. The packaging must not be pierced with sharp objects. When removing a filter from its packaging, avoid touching the delicate filter medium. Prior to assembly, each filter should be checked visually for any transport damage. Damaged filters should not be used. each filter should be checked visually for any transport damage. Do not use damaged filters.
Disposal
Air filter products must not be assessed by technical/ economic criteria alone. They also need to satisfy ecological requirements.
To obtain a reliable assessment of the ecological criteria, material and production must be assessed and balanced regarding energy, influencing substances and emissions over the entire life cycle.
Composite materials, e.g. mixtures of aluminium, steel and plastics, are not recommended as they involve a higher expense of disposal. Filter systems for the separation of hazardous substances should have the smallest possible number of stages (unless otherwise required for application specific reasons) as the replacement and disposal of several contaminated filters is more expensive due to the extra time required for contamination-free filter change and due to the higher disposal costs involved (hazardous waste).
Recycled or recyclable, low-emission materials shall be preferred for filter frames.